Machining guide: Definition and types of machines
Machining is at the heart of industrial manufacturing. This process enables the production of parts with precise dimensions and perfect finishes. Used in many sectors, from aeronautics to automotive and precision mechanics, machining guarantees the transformation of raw materials into functional components. In this article, SAMO explores machining and its machines.
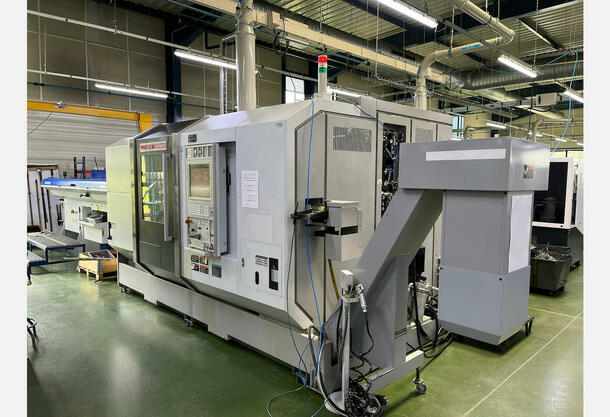
Definition: what is the principle of machining?
Machining is a manufacturing process that consists of removing material from a raw block to give it a defined shape. This process is based on different techniques, both traditional and modern.Machining by removal of chips is broken down into different stages such as turning, milling and drilling.
Machining by abrasion, on the other hand, uses methods such as grinding and polishing to improve the surface finish.
Other types of machining. There are also unconventional machining technologies, such as electro-erosion, water jet cutting and laser machining. They are used for materials that are difficult to work with and require high precision.
What is the role of machine tools in the machining process?
Machining tools are at the centre of the manufacturing process. They transform raw materials into machined parts with exact dimensions. The repeatability and precision of the operations are two advantages that they bring to a company. Depending on the type of CNC machining you want, these machine tools can be conventional or numerically controlled. The latter offer advanced automation of tasks.
What are the different types of machining equipment?
Several machine tools allow the removal of material:- The CNC lathe allows a mechanical part to be rotated around its axis while automatically controlling the cutting tool to remove shavings evenly. It is used to produce cylindrical parts with high precision, optimising mass production and repeatability of shapes.
- A ‘milling machine’ is an automated machine tool that uses a digital control system to machine parts with precision. It works by removing material using a rotating milling cutter according to a pre-established programme, enabling the production of complex 2D or 3D shapes in various materials such as metal, wood or plastic.
- A drill press is a fixed machining machine used to drill precise holes in various materials. Guided by a vertical column, it offers optimal stability and control, ensuring precise and repetitive drilling.
- Grinding machine: Machine that refines the surface of a part by eliminating irregularities using an abrasive wheel.
- Electrical discharge machining (EDM): Machine that machines conductive metals by means of electrical discharges without direct contact with the tool.
- Laser cutting machine: Uses a laser beam to cut materials with high precision.
- Water jet cutting machine: Cuts materials by projecting a high-pressure water jet, sometimes mixed with an abrasive.
- Folding machine: Machine used to deform metal sheets by giving them a precise angle without cutting them.
- Guillotine shears: Machine used to cut metal plates in a straight line with a moving blade.
- Hydraulic press: Exerts a controlled force to stamp, bend or assemble materials.
These machines require human intervention for positioning and execution of operations.
Numerical control machines (CNC) have revolutionised machining! And for good reason, CNC machining brings increased precision and complete automation of the process. Capable of following predefined computer programmes, these machines are profitable for industrial series.
CNC machining centres combine several functions (milling, drilling, tapping) in a single unit, thus optimising productivity.
Advanced cutting machines, such as those using lasers or water jets, enable high-precision machining without direct contact with the material, thus limiting tool wear.
How do you choose the right machining machine for your needs?
The choice of a machining machine is based on several decisive criteria. The nature of the materials to be worked directly influences the type of machine and tools required. The precision required in the manufacture of parts is also a key factor: while conventional machines are sufficient for simple parts, CNC machines are preferable for more stringent requirements. Production volume also plays an important role: mass production requires highly automated machines, while prototyping units can operate with more flexible equipment.SAMO, the machine tool specialist in France
With the evolution of technologies, machining processes are constantly being perfected. They offer companies real gains in productivity and better energy efficiency. SAMO offers a wide range of used machine tools and spare parts for lathes or grinding machines to optimise your production thanks to high-performance machining solutions tailored to your needs.